HOLZ-HER ZENTREX 6215 dynamic: For automated charging in combination with panel storage system
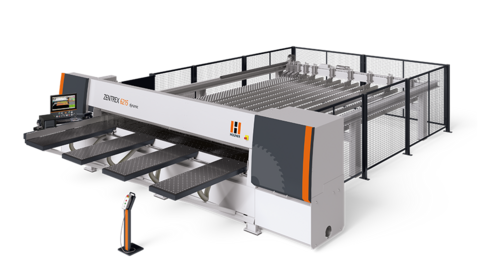
The ZENTREX 6215 dynamic horizontal pressure beam saw is HOLZ-HER’s optimum solution for link to storage of the high performance panel saw. The ZENTREX 6215 dynamic is the perfect match for the HOLZ-HER STORE MASTER 5110 panel storage system, and is particular attractive as a complete package for automating processes in your workshop.
With a saw blade protrusion of 130 mm, the powerful drives and variety of intelligent control features, the ZENTREX 6215 is inspiring even for mass production cutting. Unique on the market: The high quality linear guide technology installed on all axes.
Thanks to the high feed rates up to 150 m/m on the sawing carriage and the steep acceleration ramps, the HOLZ-HER pressure beam saw achieves the shortest cycle times in addition to an extremely high level of precision. In addition, the automatic cutting length system controlled via the optimization software minimizes the processing times of all cutting patterns.
The permanent “Continuous Check-Up” feature guarantees a cutting accuracy of 0.1 mm over the entire length and breadth of the cut.
Different requirements - different prices
The price of a HOLZHER machine is just as individual as your requirements are. Therefore, let us discuss briefly what is most important to you – you will then receive our preliminary, non-binding quote.
Personal advice – for higher productivity and greater efficiency
Together with your HOLZHER expert you will find the ideal machine for your requirements. Simply submit the completed form, and your local HOLZHER expert will be happy to discuss all further details with you.
This is what the HOLZ-HER ZENTREX 6215 dynamic offers
- Prepared for charging solutions
- Saw Blade Protrusion: 130 mm
- Sawing Unit: up to 25 kW
- Cutting Lengths: up to 5,800 mm
- Cutting Widths: up to 6,500 mm
Technical Details
Prepared for charging solutions
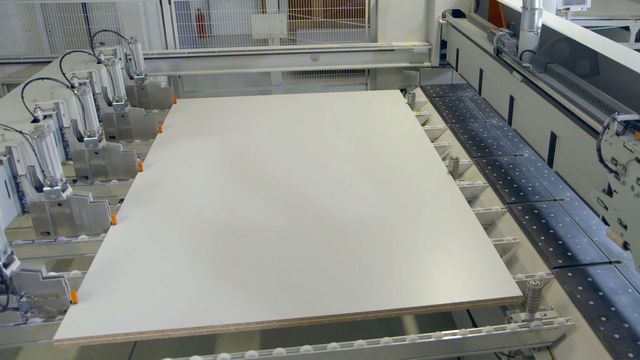
Prepared for profitable, state-of-the-art charging solutions
HOLZ-HER storage systems offer fully automated and intelligent processes as well as highly efficient use of available storage space. Sophisticated fully-integrated software with chaotic storage management increases production capacity enormously. From manual charging to automatic panel handling from a horizontal storage facility. The ZENTREX 6215 dynamic is perfectly prepared for mature solutions as well as for all sizes of shops and all types of applications.
- Extended cutting width of 6,500 mm - allows the next panel or next stack of panels to be fed to the saw simultaneously while cutting is in progress. This eliminates waiting times and guarantees cutting cycles at maximum speed. It also allows large panels to be cut crosswise.
- Liftable, floating-type workpiece clamps - with linear guide allow compensation of irregularities in panels/stacks. The clamps are moved automatically to their highest position at the rear area of the machine for prestacked panel stacks. This allows the clamps to move over the stack of panels, grip the stack and move it toward the cutting line.
- Two standard longitudinal alignment units - for high speed, automatic alignment of panels or stacks.
- Additional roller tracks - prevent remnants or thin panel material from sagging.
Laser supported positioning system
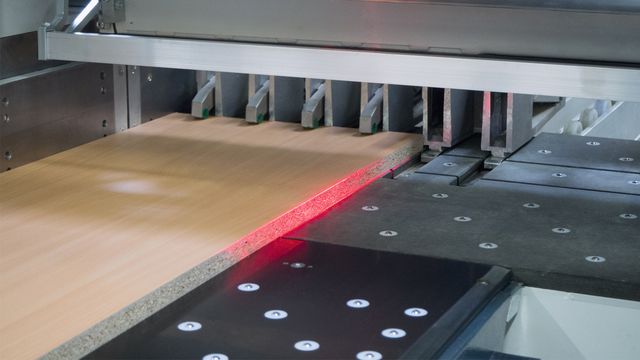
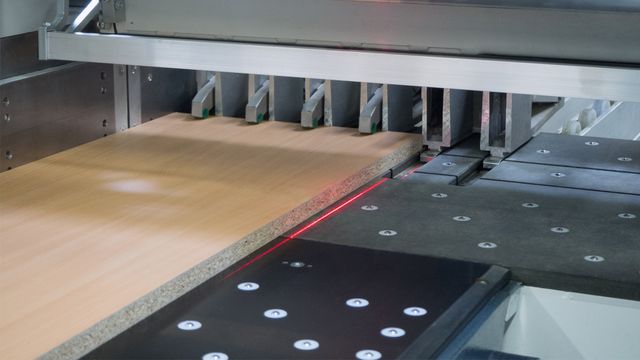
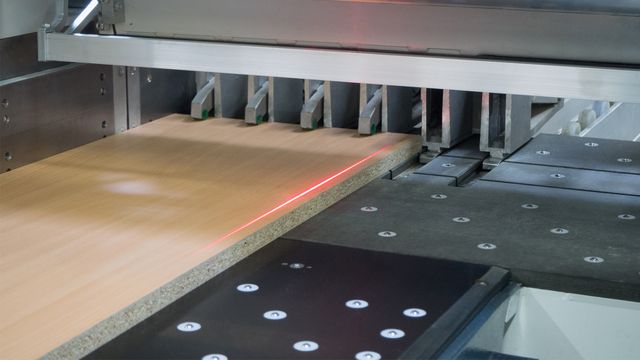
Laser-supported display system for error-free part identification.
For panel sizes, whose length is difficult to differentiate from its width in spite of 3D simulation, the ZENTREX 6215 now offers a laser positioning system with accuracy down to the millimeter. Your advantage: Remeasuring panels or incorrect positioning in the machine is a thing of the past. Moreover you minimize incorrect cuts and reject parts.
2-stage evacuation management system
Maximum evacuation power using synergistic effects of individual “Dust Control” and “Clean Protection” features
Dust Control – for program-controlled evacuation
The cutting position recognition feature optimally controls all evacuation openings in the pressure beam. This always ensures maximum evacuation power directly at the saw blade, keeping your machine table free at all times. Evacuation openings not required are closed automatically - can, however, be adapted manually on the control to ensure your machine table is always clean.
Clean Protection – for scoring cuts
When making scoring cuts, an intelligent, moving evacuation unit behind the saw blade prevents chips and dust from being hurled out unchecked during the cutting process. This keeps your machine table clean even during extremely narrow scoring cuts.
Control Center
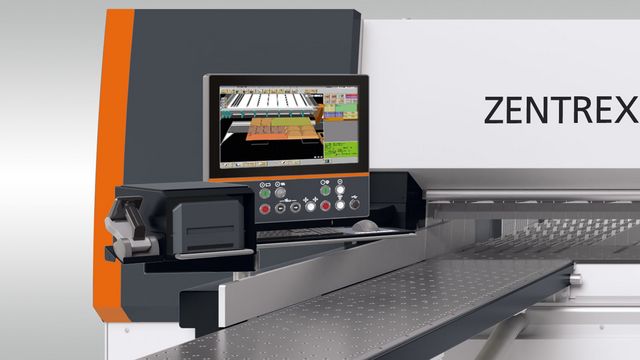
A perfectly designed workplace provides the basis for efficient, non-fatiguing work. With the 21.5" control terminal HOLZ-HER panel cutting saws satisfy all requirements placed by machine operators. The ergonomically adjustable rack offers space to position up to two printers, scanner, keyboard and mouse where they are located perfectly for the operator.
The control center with large multi-touch 21.5” full HD monitor with 16:9 format guarantees maximum clarity with real time 3D graphics and full graphic finalization help.
The CUT CONTROL 2 control package
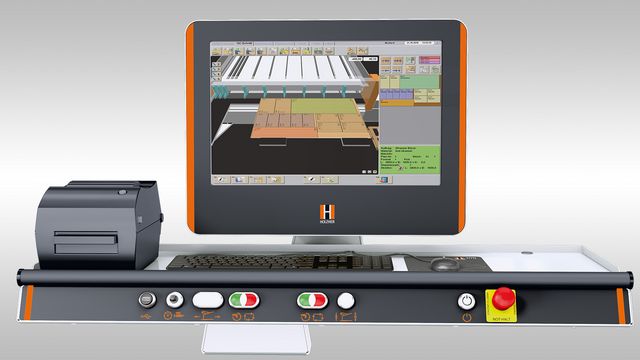
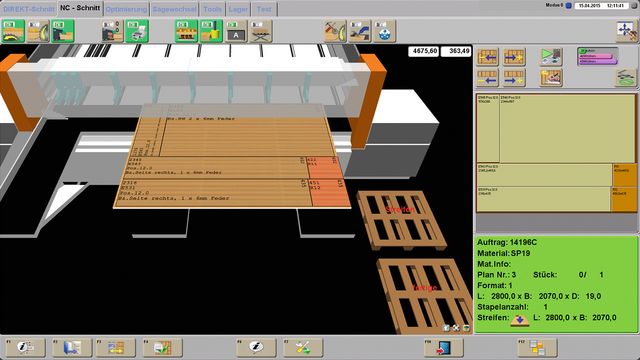
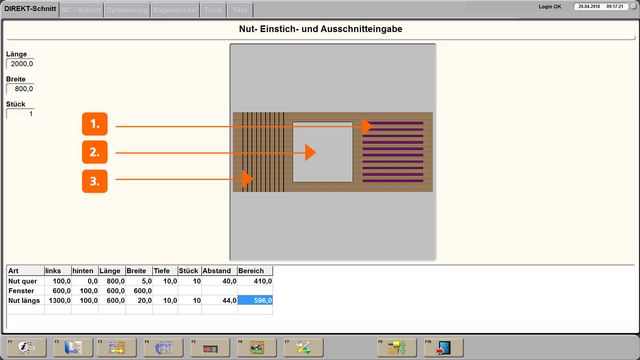
The high performance software package for large HOLZ-HER industrial saws
The control is decisive for the power output of a state-of-the-art pressure beam saw. The ZENTREX series is controlled by our CUTCONTROL 2 and the preinstalled EASY-PLAN and OPTI-CUT software packages.
Everything at a glance:
- Standard, large 21.5" monitor (with optional touchscreen) and large, clearly arranged buttons make it possible to machine absolute, series and format cuts with integrated groove.
- OPTI-CUT and EASY-PLAN optimization software is installed on the machine at the factory.
- Individual jobs can be assigned a priority at any time, job programming parallel to cutting.
- A feature for importing .CSV files is included as a standard feature.
- Graphic 3D user interface for intuitive operation and machine sequence functions for NC cutting.
- Program-controlled measurement of reference dimensions when saw blade is changed.
- Information display indicating running meters for main and prescoring saws.
- Individual adaptation of function and parameter settings.
- Label printer (optional) for barcode labels (also data matrix barcode incl. software module for creating labels).
Direct cutting capabilities
1) Longitudinal or transverse starting grooves
2) Window cutouts
3) Longitudinal or transverse grooves
Cutting line closure devices
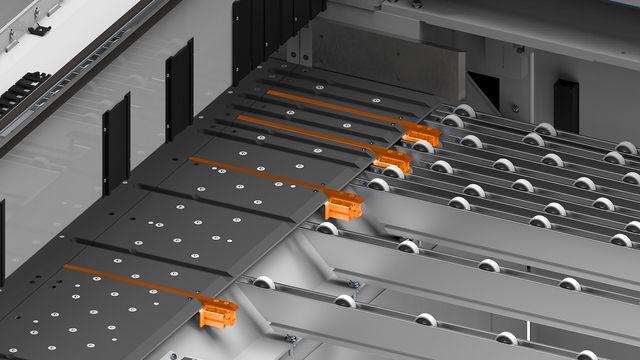
The cutting line closure devices prevent trim cuts or narrow strips from falling down and jamming in the saw slot and the saw carriage. The strips can be easily removed by the operator directly after the cut. The cutting line closers are all individually controlled and close after the saw blade has passed by. The process takes place automatically via the control system.
TwinPress – two-sided angle pressing device
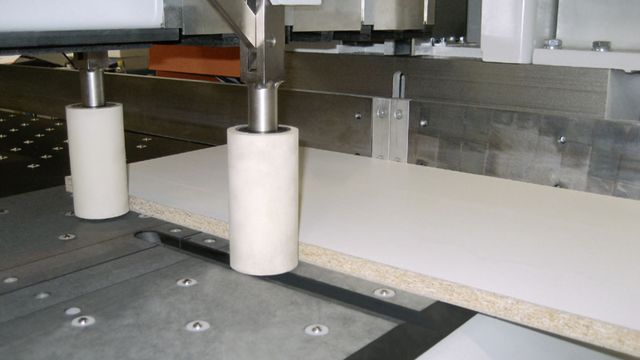
Two-sided angle pressing device (program-controlled) - for short cycle times
Scope of functions:
- TwinPress – applies pressure to both sides of the workpiece in front and in back of the sawing line
- Servo-controlled – automatically pre-positioned
- Infinitely regulated pressure (starting with 0 Nm) for thin and easily deformed materials. It is possible to simply position the angle presser unit on the workpiece without pressure.
- Alignment width: 35 – 2,200 mm for gentle material handling
- The rotating pressure roller prevents damage to the workpiece
Line laser for cutting line
The Visible Cut Line uses a laser beam to indicate the exact cutting line. This also allows cuts according to a manual sketch to be positioned and cut perfectly. Naturally this device also provides a major advantage when cutting real wood (e.g. edging).
Powerful sawing units up to 21 kW
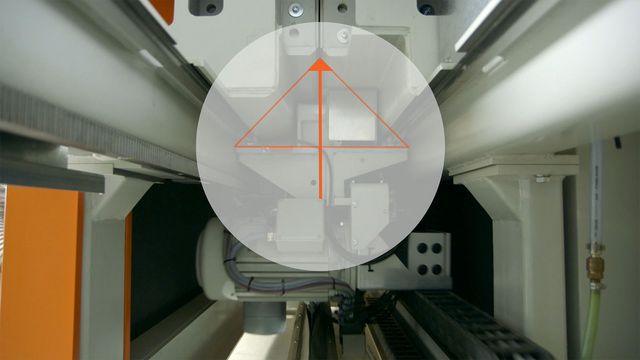
High Power – Extremely Smooth Operation
The patent-pending sawing unit is distinguished by its performance, precision and enormous cutting power. The servo-motor with recirculating ball spindle from CNC technology moves the saw blade to the desired height in seconds. During this operation the high power main motor remains in its fixed position and is no longer raised. This allows the saw to be moved infinitely to grooving depths and saw blade protrusions up to 115 mm at enormous speed. Panel stacks can be cut easily by the high power motors. The main and prescoring saw blade is guided by a linear guide as it moves up and down.
The prescoring saw can be adjusted under program control using the servo-technology. A postforming unit for material thicknesses up to 50 mm with drive power of 2.2 kW is also available as an option.
The solid layout of the machine column and ideal triangular power transfer together with ground and hardened linear guides and brushless servo-drives on all axes allow massive stacks to be cut to perfection.
Perfect triangle of forces
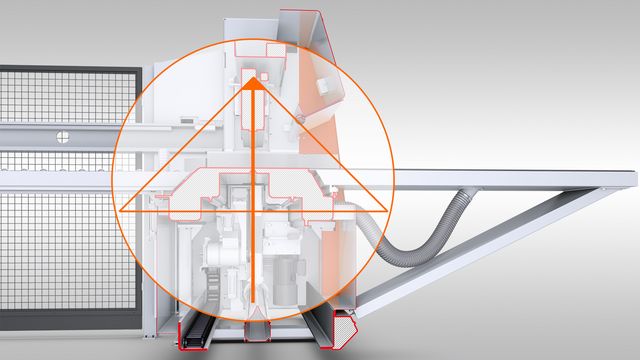
The HOLZ-HER sawing unit runs on hardened and covered linear guides as a standard feature. The guide is located precisely where the panel material is being sawed.
The cutting forces are dissipated linearly in the middle of the sawing unit. Perfect power triangle at the cutting line for permanently ideal sawing performance thanks to sophisticated design of the sawing carriage guide and maintenance-free rack-and-pinion drive.
Security Package

Our new "Security Package" guarantees particularly safe operation on and around the machine!
- Soft-start workpiece clamps
- Safe line in area of pressure beam
- Double check for all safety-relevant functions.
Our optional Security Package includes a second computer and an uninterruptible power supply (UPS).
For intelligent sawing
Automatic, infinite cutting height adjustment
- The optimum saw extension is calculated using the stack height measured by the pressure beam and the adjustable saw blade protrusion.
Optimized automatic cutting length feature
- The sawing carriage is controlled by this optimization feature. The start and end of the cut are calculated, allowing the sawing carriage to be prepositioned beneath the panel.
Motor-driven groove height adjustment
- Adjustable groove depth from 0 - 110 mm programmable on control and optimization. Adjustment is accomplished using a recirculating ball screw in the 0/1 mm range, including grooving software with graphic support.
- The bidirectional grooving feature (FCM - Fast Cut Mode) - achieves the shortest possible cycle times for grooving. Grooving is accomplished when moving backward as well as forward.
Electrical prescoring saw adjustment
- Allows simple and perfect adjustment of the prescoring saw on the monitor, in the shortest possible time, with minimum effort.
- The positions of the saw blades in relation to the tool and then to the material are saved, eliminating additional adjustment work when changing tools for various materials, etc.
- The grooving and cut-out equipment allows grooves, window or corner cutouts to be made including programming software with graphic support.
Intelligent workpiece clamps
- The floating clamps included as a standard feature with their intelligent, software control provide a plethora of benefits including reduced cycle time, improved cutting quality and gentler material handling. The clamps are switched on automatically and individually by the cutting plan. Advantage: No damage to outer panel edges because workpiece size is checked beforehand by the software. This saves a great deal of pneumatic energy, because only the clamps actually required for clamping are used.
Angle pressing device, double version
- The alignment force is automatically preprogrammed using the material (parameters) and stack height for optimum prepositioning. This eliminates waiting times when aligning the panel strips against the angle guide. Infinitely regulated pressure (starting with 0 Nm) for thin and easily deformed materials. It is possible to simply position the angle presser unit on the workpiece without pressure.
Freely programmable rip fence
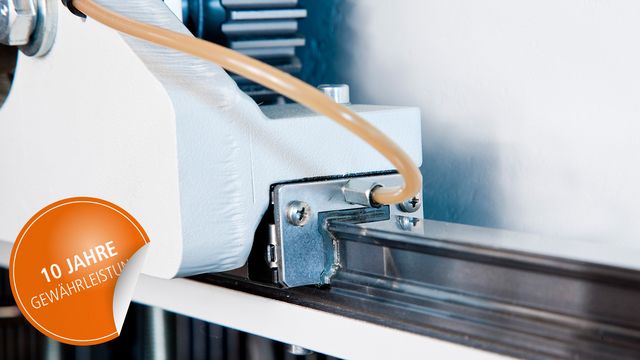
Precision guided, freely programmable rip fence on linear guide with dynamic servo-drive. Up to three double finger clamps in stop area allow narrow strips to be cut simultaneously. Floating-type workpiece clamps compensate for tension in the panel stacks toward the top.
Remnant cutting device integrated into the pressure beam
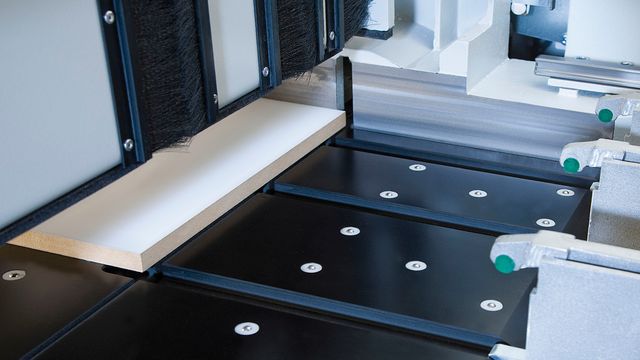
Remnant cutting device in pressure beam - the clamps retract into the grooved pressure beam. This allows panels to be cut completely without remnants for perfect utilization of the entire panel.
Floating workpiece clamps
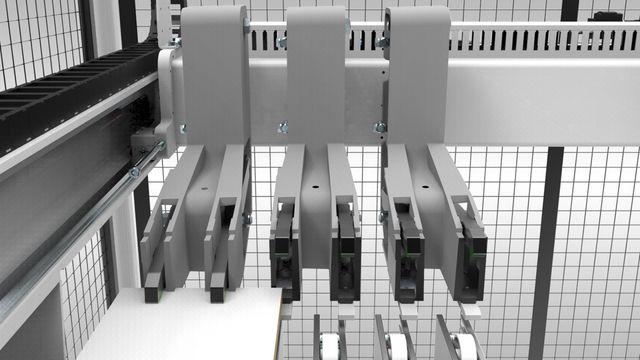
The floating clamps included as a standard feature with their intelligent, software control provide a plethora of benefits including reduced cycle time, improved cutting quality and gentler material handling.
- The clamps are switched on automatically and individually by the cutting plan. Advantage: No damage to outer panel edges because workpiece size is checked beforehand by the software. This saves a great deal of pneumatic energy, because only the clamps actually required for clamping are used.
- Automatic, infinite pressure control using material parameters.
- The included Security Package provides a safety switch-off in the front access area - ensuring maximum safety for you and your machine operator.
Solid air cushion tables
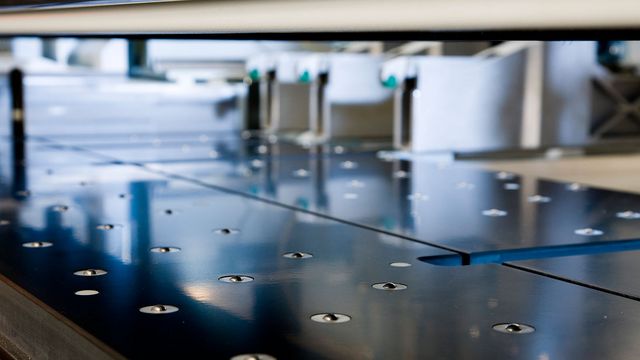
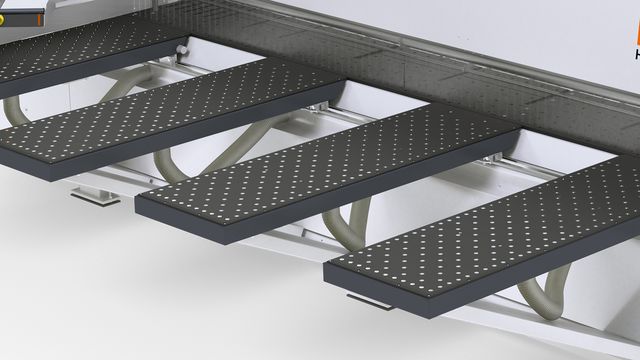
High functionality – perfect ergonomics
The equipment and possible options on the ZENTREX 6215 are defined by demanding industrial standards.
- The machine table is equipped with air nozzles to form an air cushion before and after the sawing line, ensuring easy and gentle panel handling.
- The support tables can be moved very easily for workpieces with small dimensions or to obtain additional space.
- The air cushion tables (1,800 mm) are supported directly on the body of the machine and can be adjusted - on the mobile version - easily to the material dimensions and height of the operator.
- Extremely stable design of air cushion support tables for exceptionally heavy stacks of panels.
- Lateral and front mounted feed rollers on the support tables provide for smooth, ergonomical and easy feed to the saw (optional).
EASY-PLAN optimization module

EASY-PLAN – the name is the program
The EASY-PLAN optimization software installed as a standard feature provides all functions, such as:
- Entry of material data and parts list data
- Job summary
- Cutting plan survey for optimized jobs (representation at one level)
- Manually turning for individual parts or entire raw panel
- Freely selectable front and veneer pattern applications (with Drag and Drop).
- Material-related result display in graphic form.
- Display provides information on required material formats, panels and remaining formats per job.
- Complete jobs can be reset and booked back into the parts list at any time.
- Full access to remnant management
The material data entry provides information on length, width and thickness of the material, quantity present in stock, turnability in consideration of grain pattern, material designation, type number and trimming. The parts list data includes the element number, position number, quantity, length and width.
OPTI-CUT optimization module
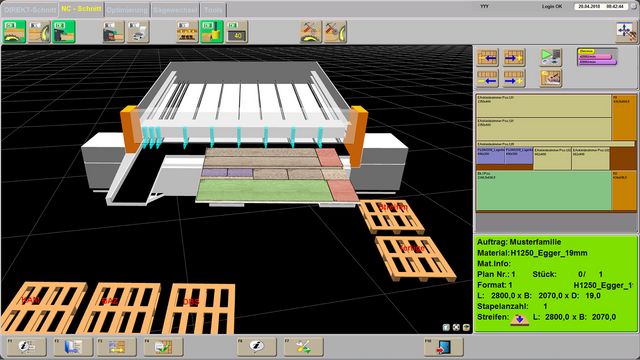
OPTI-CUT – makes your work even easier
The OPTI-CUT software preinstalled on your machine serves for creating, managing and optimizing jobs. This integrated optimization software is also available as the OPTI-BASE office version.
- The software supplies current job information for NC cutting.
- An additional module imports parts lists from user programs via the CSV interface.
- Simple configuration of all system settings.
- Material-related result display of optimized parts lists in graphic form.
- Layout and management of edging lists with predefined edging recommendation lists.
- Defined cutting length adaptation from the software significantly reduces cycle times.
- The remnant storage feature manages your remnant material and saves you the trouble of searching for materials.
Optimization module OPTI-PRO

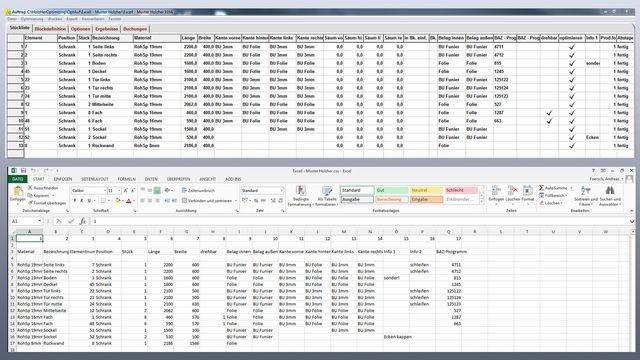
OPTI-PRO – premium optimization
The premium version with a variety of additional modules and useful functions. This optional office optimization package for sawing software is equipped for high speed data input as well as simple import of cutting data from branch or ERP programs via CSV interface. The OPTI-PRO Software performs a number of useful calculations including the cutting time for the optimized cutting plan as all as the quantity of edging to be ordered including material price. Front and veneer pattern applications can be reviewed in the office as so-called block parts. The Drag and Drop feature allows any desired individual parts to be moved to the desired front projection. The software automatically takes over other functions such as rod and strip optimization or integrated insertion of standard workpieces to be put into stock. The OPTI-PRO package is rounded out by batch jobs and other functions.
Technical Details
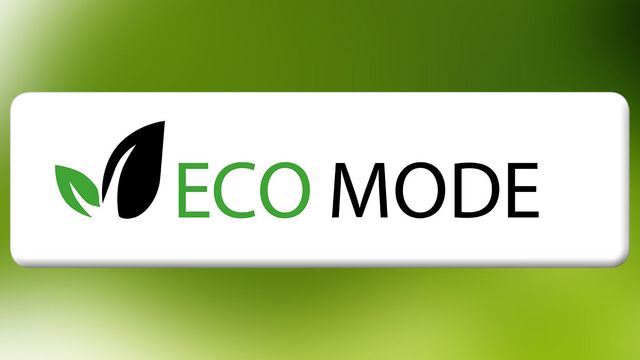
Energy savings made easy
The intelligent ECO MODE energy management for HOLZ-HER pressure beam saws not only helps preserve our environment - it also saves you money.
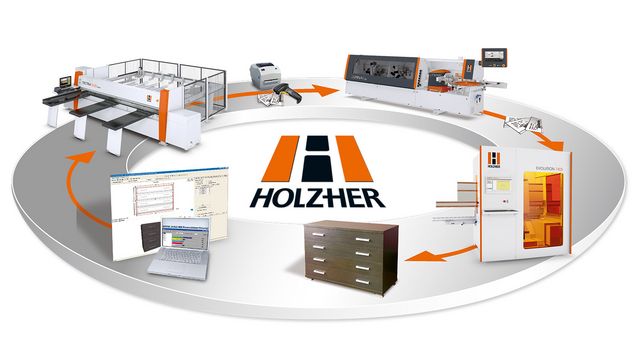
Maximum efficiency with Holz-Her machine networking
HOLZ-HER realizes your production ideas within 20 minutes from the first mouse click to finished furniture with seamless machine networking.
Further information
Brochures
Simple, fast and sustainable: more details in a downloadable PDF document.
Brochure ZENTREX 6215 (PDF, 944 KB)